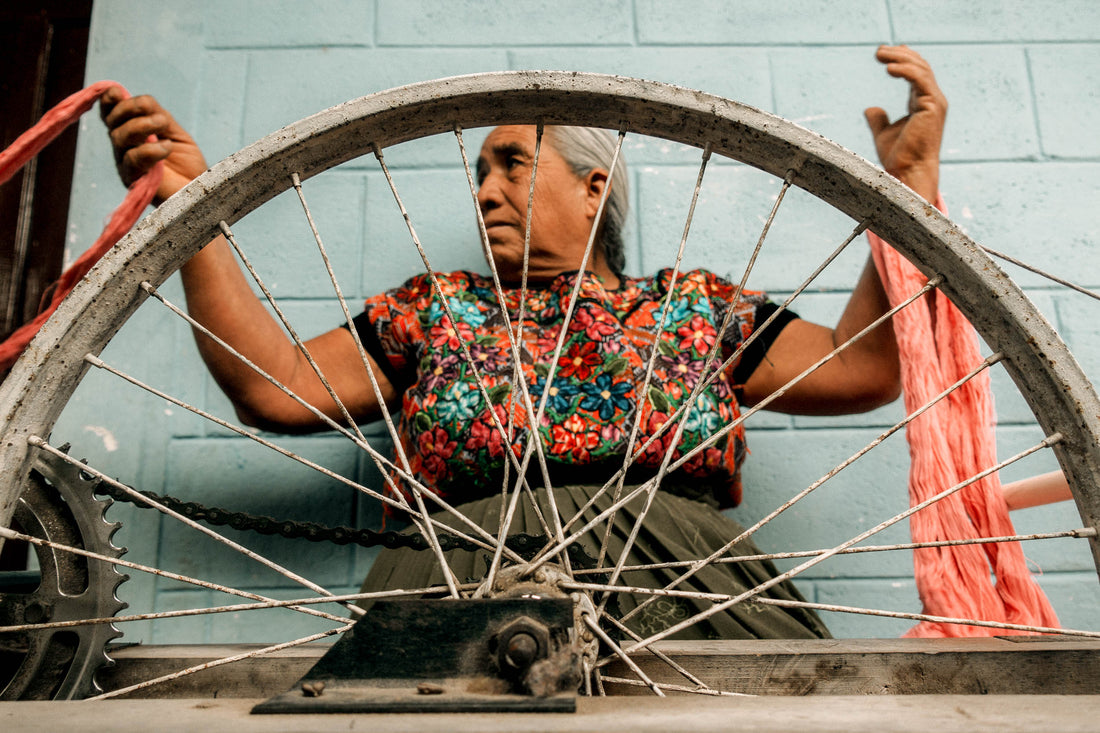
The Footloom Process Simplified
Our Artisan Collection is one of our most important collections, as it was created to encourage and support the art of weaving. This collection of newly woven fabric is made custom using a footloom, and it's created on a small-batch scale ensuring attention to detail and quality. Commissioning the looming of these new fabrics is key to the local economy, because it creates a sustainable form of income and encourages tradition. With your help we are able to keep this beautiful art form alive, and support the well-being of our beloved Guatemalan artisans!
1. Thread for weaving is purchased in skeins (loosely coiled lengths of thread), and then placed onto a handmade device called a devanadora. The thread is then transferred onto smaller metal spools using a spindle, called a ruedina, which is usually made from a metal bike wheel.
2. The spools of thread are aligned by color on a long rectangular device called a cañonera, which helps organize the order of color required by the fabric design.
3. The weaver then separates and organizes the threads piece by piece using her fingers and hands. Then she sorts the desired pattern onto another handmade spinning piece of equipment, called an urdidora, that stands taller than herself.
4. The organized thread then goes through a piene (comb-like device) to determine the thickness of each section.

5. The thread is then mounted onto the footloom. It’s finally ready to weave!
6. The foot pedals control the threads that move up and down as the weft (the horizontal thread) is passed through the warp (the vertical thread). The weavers work simultaneously with their hands and feet to create the fabric you see on the bags.